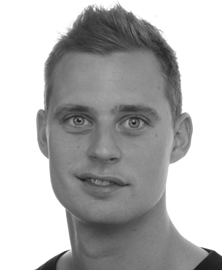
Projektet adresserar utmaningen som tillverkarna av elektromobilitetskomponenter möter. Att nå en balans mellan kvalité, tid och kostnad.
Bearbetning av tunnväggiga komponenter med låg styvhet såsom stringers och statorhus i elektriska fordon är alltid en utmaning för tillverkare eftersom komponenterna lätt deformeras under bearbetningen på grund av skärkraften. Därför utförs deras bearbetning normalt genom flera steg istället för ett enda steg. Till exempel grovbearbetning, halvbehandling och efterbehandling.
I varje steg måste ingenjörerna bestämma många saker, såsom de material som behöver skäras och deras skärsekvens, de nödvändiga tillverkningsresurserna inklusive maskiner, fixturer och skärverktyg med lämpliga skärparametrar. Under tiden är oron för varje steg annorlunda. Till exempel förväntas de flesta material skäras genom grovbearbetning på ett snabbt sätt eftersom det inte finns något kvalitetskrav i detta skede, medan skärparametrarna vid efterbehandling måste väljas noggrant eftersom de kommer att avgöra den slutliga bearbetningskvaliteten. Men varje steg fungerar inte irrelevant. De är faktiskt kopplade till varandra.
Som ett resultat kämpar tillverkarna för att skapa en bearbetningsprocessplan som kan nå en balans mellan bearbetningskvalitet som skildras av snäv tolerans, bearbetningstid och bearbetningskostnad. I denna forskning, utöver vår förståelse för fysik för metallbearbetningsprocessen, kapaciteten hos datorbaserade tillverkningstekniker som CAD / CAM / CAE och optimeringstekniker, har vi skapat ett virtuellt fysikaliskt simuleringsverktyg för att hjälpa processplanerarna att undersöka hur processparametrarna påverkar komponenternas bearbetningskvalitet.
Genom att koppla ihop det utvecklade simuleringsverktyget med optimeringsfunktion kunde de optimala kombinationerna av processparametrar hittas för att uppnå en balans mellan bearbetningskvalitet, bearbetningstid och bearbetningskostnad. Under tiden kan det nuvarande fysikaliska experimentbaserade trial-and-error-bearbetningsprocessplaneringsläget flyttas till ett virtuellt simuleringsbaserat optimeringsläge.
Följaktligen kommer företagen att spara mycket material och tid som behövs av de fysiska experimenten.